Closed System Water Treatment Problems: Corrosion
Posted by David Cannon on 4th May 2017
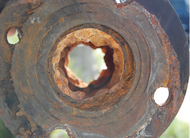
Some of the leading conditions that can cause problems in closed systems are:
Leaks. Water loss, either through leaks or intentional releases, will drain away any chemical corrosion protection and introduce fresh, oxygen rich, water. When fresh water enters a closed system the dissolved oxygen will react with metals such as iron and copper. When oxygen reacts with iron it forms iron oxide (rust) that can expand the thickness of the iron by up to 20 times.
Exposure to atmospheric oxygen. Approximately 20% of the atmosphere is oxygen. If the water in a closed system with an open tank is exposed to the atmosphere, oxygen can easily enter the system and accelerate corrosion. In addition to closed system deposit and corrosion inhibitors, adding biocides to control biological growth is advised.
Corrosion increases with stagnation. In closed systems where the water remains stagnant for long periods of time there is an increase in corrosion. It is better to circulate the water and maintain a protective chemical concentration in all sections of a closed system. Periodically running the circulation pumps at least weekly and maintaining treatment levels will help reduce the corrosion.
Deposition. Corrosion deposits in one area can migrate to other areas and plug pipes, control valves and heat exchangers. Consider chemical cleaning (see below) and filtering the water.
Corrosion deposits can cause wear and tear on seals and pumps.
Moderate Cleaning Process:
- Add a borate nitrite treatment to 1500 ppm as sodium nitrite and test the water.
- Circulate the water for at least 24-hours.
- Start a bleed on the closed system and flush the water to sanitary sewer while running the circulation pumps until the nitrite level drops to 500 - 700 ppm as sodium nitrite. Testing can be performed by using our Nitrite Test Kit CNTK3300-Z
- Repeat the process by adding the borate again and re-flushing after 24-hours.
Filter in addition to chemical cleaning.
- Install a 1 to 5 micron filter on a bypass to the circulation pump and check the filter daily. Replace or clean the filters when noticeably fouled. We recommend the Vector 7 Gallon Filter-Feeder with 5 micron filter sock.
- If there is an open tank, suction out any deposits that may be deposited on the bottom of the tank.
- Plan to use the filter as a permanent means of keeping the closed system free of entrained particles, checking the filter element periodically to see how much particulate is being captured. This should diminish over time.
More Aggressive Cleaning Process.
- Add a polymer iron dispersive/cleaner such as our Eco-Green Ferro Kleen.
- Follow the guidelines for cleaning using Ferro Kleen.
Corrosion and corrosion deposits develop over time and they are difficult to remove in one cleaning process. It may take repeated cleanings to get most of the iron oxide and sludge out of the system.
Protecting the system from further corrosion:
Immediately after the system has been cleaned and flushed a corrosion inhibitor must be added to prevent corrosion from developing. Corrosion begins within minutes of being flushed out due to exposure to fresh oxygen in the water. Many contractors wait too long to chemically treat the system after flushing causing the system fluid to turn grey from iron oxide corrosion. While this is not detrimental to the system it will look dirty. Add corrosion inhibitors immediately to prevent this. We recommend the installation of a by-pass feeder on the closed loop to allow for chemical to be added to the system. Systems without a by-pass feeder almost never get proper chemical treatment and usually fail after just a few years. A properly treated system will last for the life of the building.
Corrosion Inhibitors:
Typical corrosion inhibitors for closed loops will contain nitrite that acts as an oxygen scavenger. Once the nitrite has completely reacted with the oxygen in the system much of the nitrite will convert to nitrate as it absorbs oxygen molecules. This is the basis of corrosion protection for the majority of closed loops around the world. Nitrite also acts as a film protection for the surface of iron pipe, further protecting it from corrosion.
Tolyltriazole compounds are another additive that is commonly used in conjunction with nitrite. This additive is often referred to as 'Azole' or 'Toly' among water treaters. Tolyltriazole is used as a filming type corrosion inhibitor for yellow metals like bronze, brass and copper. Many formulations include this with nitrite and is fed proportional to nitrite so you will just need to maintain your nitrite levels and the tolyltriazole will be dosed at the correct level.
Molybdate is another common corrosion inhibitor that was used for decades. In recent years it has been phased out almost completely around the world as prices for molybdates rose to ridiculous levels. Molybdates are synergistic with nitrite which reduces the dosage required for both chemicals.
Organophosphonates are now becoming the leading choice for closed loop corrosion inhibitors due to their low cost and excellent filming properties. They are not considered an oxygen scavenger so these inhibitors can be used in open systems that are exposed to oxygen without the fear of being depleted over time. Testing is done with an OP test kit. We recommend our CNTK0159-Z test kit.
We can provide everything you need to properly clean, treat and test your closed loops.
Typical savings of 40 to 70% can be expected when using our chemical formulations.
Please contact us for a free consultation. We will evaluate your system and provide feedback on what is the best course to take.
Richard S. Cannon
AWT Certified Water Technologist # 1253