How Injection Quills Provide Safety While Handling Chemical Injection?
Posted by David Cannon on 10th Sep 2023
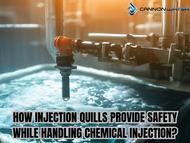
Chemical injection refers to the controlled introduction of chemicals, additives, or reagents into a fluid stream, typically a liquid or gas, in a precise and measured manner. This process is widely used across various industries and applications for a range of purposes, including water treatment, industrial processes, oil and gas production, pharmaceutical manufacturing, and environmental remediation.
Chemical Injection Serves Important Functions:
- Water Treatment: Chemical injection is commonly used in water treatment processes to improve water quality. Chemicals may be added to remove impurities, disinfect, adjust pH levels, control corrosion, and address specific water quality issues.
- Industrial Processes: Many industrial processes require the addition of chemicals to facilitate reactions, control process variables, enhance product quality, or achieve desired outcomes. For example, chemical injection may be used in chemical manufacturing, food processing, and metallurgy.
- Oil and Gas Production: In the oil and gas industry, chemical injection is employed for various purposes, such as corrosion inhibition, scale control, hydrate prevention, and enhanced oil recovery (EOR). Injected chemicals can help maintain the integrity of pipelines and equipment and improve the efficiency of extraction processes.
- Environmental Remediation: Chemical injection is used in environmental remediation efforts to treat contaminated soil and groundwater. Specific chemicals may be injected to break down or neutralize pollutants.
- Pharmaceutical Manufacturing: In pharmaceutical production, precise chemical dosing is critical to ensure the quality and consistency of pharmaceutical products. Chemical injection may be used in drug synthesis, purification, and formulation processes.
- Agriculture: In agriculture, chemical injection systems are used for the precise application of fertilizers, pesticides, and herbicides to optimize crop yield and protect against pests and diseases.
- Water Disinfection: Chemical injection is often employed to disinfect drinking water and wastewater, using chemicals like chlorine, ozone, or ultraviolet (UV) disinfectants.
Chemical injection systems are designed to ensure the accurate and consistent delivery of chemicals into the fluid stream. These systems may include pumps, meters, tanks, valves, controllers, and injection quills. The choice of equipment and the injection method depend on the specific application and the requirements for precision and control.
What are Injection Quills?
Injection quills are specialized devices used in industrial applications to safely and precisely introduce chemicals, additives, or reagents into a fluid stream. These devices play a critical role in various processes, including water treatment, chemical dosing, pH control, and corrosion inhibition. Injection quills are designed to ensure that the injected chemicals are uniformly dispersed within the fluid, preventing direct contact with the pipe or vessel walls, which can cause corrosion or other issues.
Why Injection Quill are Used to Handling Chemical Injection?
Injection quills are used for handling chemical injection in industrial applications for several important reasons:
- Precise and Controlled Injection: Injection quills allow for the precise and controlled introduction of chemicals into a fluid stream. This level of control is essential in many industrial processes where accurate dosing of chemicals is critical for process efficiency and product quality.
- Uniform Dispersion: Injection quills are designed to ensure that the injected chemical is uniformly dispersed within the fluid stream. This uniformity is crucial to achieving consistent results and avoiding issues like uneven chemical distribution or localized concentration gradients.
- Prevention of Corrosion: Injecting chemicals directly into a fluid stream using injection quills helps prevent direct contact between the chemicals and the interior surfaces of pipes, fittings, or vessels. This is particularly important when dealing with corrosive chemicals, as it reduces the risk of corrosion and extends the lifespan of the plumbing infrastructure.
- Safety: Injection quills often incorporate safety features such as check valves or backflow preventers. These features help prevent the reverse flow of fluid or chemical into the injection line, ensuring the safety and integrity of the system.
- Efficiency: By ensuring that chemicals are thoroughly mixed with the fluid, injection quills promote the efficient use of chemicals, reducing waste and minimizing the consumption of expensive or hazardous substances.
- Process Optimization: Many industrial processes require precise chemical dosing to achieve specific outcomes, such as controlling pH, inhibiting corrosion, or promoting chemical reactions. Injection quills facilitate process optimization by delivering chemicals in the right quantities and at the right locations.
- Reduced Maintenance: Minimizing direct contact between chemicals and plumbing surfaces helps reduce corrosion-related maintenance and repair costs. This is especially important in industries where downtime due to maintenance can be costly.
- Diverse Applications: Injection quills are versatile and can be used in a wide range of industries and applications, including water treatment, chemical manufacturing, oil and gas production, pharmaceutical production, and environmental remediation.
- Compliance: In many industries, regulatory agencies and standards organizations require precise chemical dosing and monitoring. Injection quills help ensure that processes meet regulatory compliance and quality control standards.
How Injection Quills Enhance Safety While Chemical Handling Injection:
Injection quills provide safety in handling chemical injection in industrial applications through several key design features and functionalities. These features are intended to mitigate risks associated with chemical injection, ensure proper handling, and protect both the equipment and personnel involved.
- Containment and Isolation: It physically separate the chemical being injected from the main fluid stream until they are properly mixed. This isolation helps prevent direct contact between the chemical and the internal surfaces of pipes, fittings, or equipment, reducing the risk of corrosion and damage.
- Backflow Prevention: Many injection quills include check valves or backflow preventers in their design. These components prevent the reverse flow of fluid or chemical into the injection line, ensuring that chemicals only flow in the intended direction.
- Chemical Compatibility: Thy are typically constructed from materials that are chemically resistant to the specific chemicals they will handle. This compatibility ensures that the quill itself will not degrade or react with the injected chemical, preventing unintended chemical reactions or hazards.
- Uniform Dispersion: They are designed to disperse the injected chemical uniformly within the fluid stream. This uniformity prevents localized high concentrations of chemicals, reducing the risk of chemical reactions or damage to equipment.
- Precise Control: It allow for precise control of chemical injection rates and quantities. This control is important in processes where accuracy is critical for safety and efficiency.
- Monitoring Points: Some injection quills feature ports or connections for monitoring and sampling the chemical being injected. This allows for real-time monitoring of chemical concentrations and ensures that the injection process is functioning as intended.
- Pressure and Flow Control: Injection quills may include flow control mechanisms, such as adjustable orifice plates or valves, to regulate the flow rate of the injected chemical. This helps maintain system pressure and prevent over-injection.
- Ease of Installation: They are designed to be easy to install in existing pipelines or systems. Proper installation is essential for safe and effective chemical injection.
- Materials of Construction: The choice of materials used in injection quill construction is critical. Materials are selected based on their chemical resistance, ensuring compatibility with the injected chemical and the process fluid.
By incorporating these safety features and best practices, injection quills help reduce the risks associated with chemical injection processes in industrial settings. They contribute to the safe and efficient operation of various processes while protecting equipment, infrastructure, and personnel from potential hazards.