Centrifugal Separators: Working Principle, Benefits, and Applications Discussed
Posted by David Cannon on 16th Oct 2019
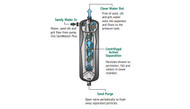
Water is found in the most impure form at stagnant water bodies and wastewater processing plants. This is because the water gets mixed with oil and chemicals as result of industrial processing. Nowadays, every industrial plant invests in wastewater processing systems. The water is treated to remove grease, chemicals and other impurities before releasing it to local water bodies. In wastewater processing, various types of filters are used. The centrifugal separator are the most popular ones. These filters are used to remove suspended solids and other impurities in water.
A centrifugal separator finds application across industries such as breweries, animal feed manufacturing, pharmaceutical manufacturing, abrasives, power generation, transportation, and ceramics. They separate cream from milk, oil from water, sand from gravel, and pigments in paints. You may wonder how centrifugal separation works. How does centrifugal separator design differ from regular separators? Read the post to know the answers.
A Brief Overview of the Centrifugation Separation Process
Centrifugal separators get their name from centrifugal force, which separates particles from the solution. This process is mainly employed to separate two immiscible substances in a solution. The centrifugal separator is spun at high speed producing high gravity centrifugal force.
Centrifugal Separator Design
A centrifugal separator features a feed pipe, a rotor, a drive mechanism, a bowl, a separation chamber, an outlet pipe, a scraper, and a control panel. The centrifugal separator diagram followed by a description of each of these parts will help you understand the design better.
- Feed Pipe: As the name suggests, the pipe is used to feed a mixture of liquid-solid suspensions, liquid-liquid mixtures, and solid/gas-liquid mixtures into the separator.
- Rotor: This separator component produces high centrifugal force by spinning. Generally, the rotor is located in the central portion of the separator. It is spun at high speed for centrifugation.
- Drive Mechanism: This may be a gas engine, a motor, or any power source, which helps power the rotor and maintain its spinning action.
- Bowl: Made of composite or metal, this bowl holds the material to be separated. It features a separation chamber, where the actual separation takes place.
- Outlet Pipe: This pipe carries the separated substances, which are released by the separator.
- Scraper: Some materials are left behind in a separation chamber or the bow, which is removed using a scraper.
- Control Panel: As the name suggests, this panel helps an operator control the centrifugation process. They can monitor the separator performance, and set the rotor’s speed.
Centrifugal Separator Working Principle
Unlike regular filters, a centrifugal separator features no filter, rather an inlet, outlet, and separator. The mixture to be separated – liquid-solid, solid-liquid, or gas-solid mixture is pumped into a cone-shaped working apparatus in the separator to produce a rotation.
The separator produces a spinning vortex, leading to solid filtration from liquids. The separated solids are collected at the bottom of the separator, and are purged from there. High-density liquid flows out of the separator and contaminants as well as low-density components will remain inside. Water is one of the denser liquids, so it flows outside, and is removed through a discharged outlet. However, low-density fluids such as oil will remain at the center of the vortex. Segregated oil can be easily recovered from the suction orifice of the separator.
An automatic or manual purge system removes separated solids in the separator. The purging duration and intervals of the automated discharge system can be easily set. The manual purge system uses a hand lever attached to a ball valve. The automatic system may be electrical.
Where Are Centrifugal Separator Used?
Centrifugal separators are available in different designs, so you can choose the one that meets your requirements. Here are a few application areas of these separators:
- Pre-Filtration: When used for pre-filtration, the centrifugal separator helps boost filtration efficiency and minimize liquid loss. Centrifugal separation helps users to save on expensive water treatment solutions.
- Protecting Heat Exchangers: Fouling is common concern in industrial facilities where heaters or coolers are used for different processes. This fouling is caused due to accumulation of materials on the surfaces of an equipment. Centrifugal separator can easily remove scale and suspended grit easily, thereby helping protect heat exchangers from fouling.
- Protecting Spray Nozzles: Spray nozzles are used to accomplish different tasks across industries. Sometimes, they get clogged with solids during operation. This affects their intended operation. This is where a centrifugal separator can help. It helps remove solids that clog the nozzles of the spray. This, in turn, helps reduce the wear and tear of the nozzle, and avoid its regular replacement.
- Reducing Industrial Waste: Oil and water mixture is a byproduct in many industries. In many cases, oil recovery or disposal of waste are both expensive. This is where centrifugal separation process can help. Centrifugal separators help separate the mixture of oil and water and recover high value solids in many applications. This also helps improve the life of seals.
- Preventing Accumulation of Debris in Basins and Sumps: The centrifugal separators are used in the cooling systems and they help minimize the accumulation of solids in sumps and basins.
What Can a Centrifugal Separator Separate?
The efficiency of centrifugal separation will depend on the difference between the specific gravity of the liquid and the solid being filtered. This separation efficiency will increase if the difference is large. The separation efficiency is also affected by the particle size. For most separators, 40 microns is considered the visibility threshold.
Get Introduced to Different Types of Centrifugal Separators
There are different types of centrifugal separator based on the designs. They are designed to separate substances based on density, shape, size and other properties. The following are some popular ones among them.
- Decanter Centrifuges: They help remove large particles from slurries with high solid concentration. Decanter centrifuges are also used to separate liquids of two phases of varying densities.
- Disc Separators/Disc Stack Centrifuges: As the name suggests, these centrifugal separators feature stacked discs. These stacked discs produce high centrifugal force, which are helpful while separating solids, and one or multiple liquid phases.
- Scroll Separators: The separators feature scroll, which helps separate solid particles of gas or liquid. The particles are spun to the scroll edge and collected.
- Hydroclones: These separators separate solid particles from liquid suspension based on their force ratio to fluid resistance. This ratio is low for fine and light particles and high for coarser and denser particles. Hydroclone separators are used in pulp and paper mills, potato processing plants, mineral processing plants, and mining industry.
Advantages of Centrifugal Separators
The Centrifugal separation process has been employed for liquid and solid separation across industries for several years now. They have no filters, bags, screens, or cartridges, making them simpler equipment when compared to many filtration equipment. In addition to their designs, these separators provide the following benefits:
- Maintenance Free: The centrifugal separator has no moving parts, which makes it essentially maintenance-free. It is fitted with an automatic purge valve designed to flush the debris and contaminants
- Minimal or No Downtime: As the filtration is performed by the spinning of a vortex, there are no real filters involved. This means there will be no accumulation of debris in filters, and no breakdown due to this accumulation. Also, there will be no need to change the filters more often, as in the case of other liquid separators.
- Minimal Liquid Loss: Do you know there is a little liquid loss by purging while using centrifugal water separators than other filters! Generally, the users bear major liquid loses when cleaning sand media filters or automatic strainers.
- High Efficiency: The efficiency of centrifugal separation is 98% of 40 microns in a single pass. However, for centrifugal separator, this is 44 microns. This stands valid for solids at the gravity of 2.6 and water at 1.0.
- Lasting Performance: Owing to all the above-mentioned reasons, these centrifugal separators assure lasting performance than their industrial counterparts. Also, if you are sourcing them from brands such as Lakos, they assure 15–25 years of service. There are various factors that contribute to the longevity of these filters. They include the environment where the separator is being used, its material of construction, type of material being separated, and so on. Most times, industrial centrifuges are made of materials such as 304L/316L stainless steel or mild steel. Brands like Lakos provide them in metals such as chrome-moly, super duplex stainless steels, nickel alloys, Hastelloy, cupronickel, and other nickel alloys. All these metals are proven to assure durability and lasting performance in adverse environments.
Areas of Application of Centrifugal Separators
Having known how the centrifugal separator work, it is quite obvious to think in which industrial process you will use the centrifugal separator? Well, they are used in various industries for separating two miscible substances. The following are a few common applications of these separators.
- Environmental Processes: Centrifugal separation process is applied in various environmental processes to separate biomass and animal slurry from water.
- Recycling: Water impurities are one of the main concerns of various recycling plants. These centrifugal separators are used for treatment and recovery processes at recycling plants. They are widely used for recycling service water in various industrial processes.
- Plastic and Chemical Processes: In the chemical industry, water is used in various phases of chemical manufacturing. Various types of byproducts are generated during chemical processes which may get mixed with water, thereby polluting the water stream. The industrial centrifugal filters help avoid contamination of water streams and recover intermediate or end products during the process. Centrifugal separators are also used during plastic manufacturing. They find great applications during PP, HDPE, and PVC polymer production. Similarly, these filters are used in minerals and ores production, pharmaceutical and biotechnology sectors, and during the production of non-fossil fuels, among others.
- Food and Beverage Production: This industry uses a lot of water and also releases byproducts during various production processes. This is where centrifugal separators can help. They are used during the processing and recovery of non-liquid food products, fruit and vegetable juice production, wine and sugar processing, among others.
- Oleo-Chemistry: Several byproducts are generated during the production of oleo-chemistry derivatives. They can be easily filtered using centrifugal separators. These separators are also used for refining edible vegetable oils. However, they are not recommended to use during the refining of olive oil.
- Mineral Fuel and Lubricating Oils: Industrial centrifugal filters are used for purification and conditioning of fuels, purification of lubricating oils, and treatment and recovery of various fuel oils. They are also used for the treatment of slop-oils from lagoons or refineries or bilge water.
- Animal-based Products: The meat and fish processing creates lots of useful and non-useful byproducts. The centrifugal separators are used for the treatment of byproducts from meat and fish processing industries.
- Milk and Dairy Products: Milk and dairy industry utilizes these filters during the production of various cheese and dairy products. They are also used for recycling the waste materials.
Tips to Improve the Efficiency of Centrifugal Separators
The right industrial centrifuge will help improve the efficiency of your separation process. However, choosing the right centrifugal separator can be challenging due to the wide range of available products. The following tips will help ease the selection for you.
- Flow Rate: Although centrifugal separators use centrifugal force to separate, their flow rates may vary. These equipment are rated by pounds per hour. The flow rate is one of the important factors for choosing the size of the separator. If you choose the separator based on the factors such as piping, then the separator may have a much slower rate than expected. If this happens, the filtration may not be complete or properly achieved. To understand the flow rate, perhaps, you can discuss with the manufacturer. Along with this, you need to use the appropriate outlet/inlet size with the piping to ensure the efficient functioning of the centrifugal separator.
- User-friendly Design: Centrifugal separators are nowadays available in different designs. However, it is not necessary that all have the same design, and assure user-friendliness. The ideal design is the one that allows a user to conduct startup, cleaning, and maintenance easily. For instance, Lakos centrifugal separators and filtration solutions feature user-friendly designs that allow users to assure easy start-ups and cleaning, whenever required. These designs are proven to filter airborne debris and suspended particles in cooling water towers, chillers, heat exchangers, and evaporative condensers.
- Set the Proper Purge Timing: Many branded centrifugal separators such as Lakos purge controllers do not have any set timings. This is because the purge duration and their frequency may depend on varying solid concentrations, flow rates, or types of solid particles, and so on. Thus, the controller times must be set according to the requirements. You can refer to the literature provided with the separator to set the purge duration and other details.
- Choose the Right Separator: Most times, the separators from Lakos and other brands assure 15-25 years of service. However, that is not enough. There are several other variables that contribute to their longevity. For instance, the material of construction, fluid or chemical used, an environment where it is used, type of solids used for purging, and regular maintenance, and so on. So, while purchasing the new separator or upgrading the existing one, all details about their utilization must be shared with the manufacturer or the supplier.
- Maintenance: Like any industrial filtration equipment, maintenance is essential for the proper functioning of a centrifugal separator. If maintenance is not properly performed, then the machine may not function as expected. So, it is important to perform maintenance on a regular basis. You can approach the manufacturer or the supplier for receiving regular maintenance. Always ensure that the maintenance is performed by an experienced professional because they perfectly understand the requirements of the device.
Now, you might have an idea of how a centrifugal separator works and how it helps separate different liquids. Thus, it is important to source them from a trusted manufacturer or a supplier. There are several centrifugal separator manufacturers and suppliers in US. Cannon Water Technology, Inc. is one of the industry-leading suppliers of centrifugal separators. The company stocks several types of centrifugal separators, chemical feed systems for industrial uses.
Our Products
![]() |
Carbon Steel Centrifugal Action Separators for Low-Flow Applications |
|
|
Lakos SandMaster Plus, Stainless Steel Centrifugal Separator Sand Removal System |
|
|
Lakos ILS Series Separators, 316L Stainless Steel Centrifugal-Action Separators for Low-Flow Applications |
|
|
Lakos LGS Series Centrifugal Separator Solids Removal Filter, 225 to 2450 GPM Flow Range |