Dosing Pump Guide - Working, Types and Applications Discussed
Posted by David Cannon on 7th Nov 2019
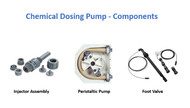
Today, various types of pumps are used for the delivery of fluids across industries. Among these several types of pumps, dosing pumps lead the list. As the name suggests, these pumps are positive displacement pumps that are designed to inject chemicals into steam, gas, or water. Over the years, they have become an indispensable part of integrated dosing systems that enable automated dispensing of chemicals. This post discusses these pumps in detail.
A Brief Discussion on the Working of a Dosing Pump
The pump draws a fixed volume of a chemical into the chamber, and then injects it into a pipe or a tank that may contain water or fluid to be dosed. The pump is driven by an air actuator or an electric motor. The electric motor is fitted with a controller which helps put the pump on or off as well as manage the rate of flow.
Know the Components of a Dosing Pump
A dosing pump is made of several components that actively contribute to its functioning. These components are described below:
- Chemical Tank: The tank is designed to hold the material to be dosed.
- Dosing Pump: A pump features an inlet, a dosing line, and a suction line. A pump varies in size and materials depending on the application. It is made of varied materials such as rubber, plastic or stainless steel.
- Injector: This is a non-return valve that is designed to inject the chemical into the flow. The injector is designed to overcome the pipe pressure, and enables easy mixing of a chemical into the liquid or product in equal doses. The injector has a self-actuated mechanism that helps avoid the liquid in the delivery line from flowing upwards, once the pump has stopped. This injector also directs the chemical delivery to the middle of the flow, thereby helping avoid product wastage, which occurs due to incorrect dosing of chemicals on the side walls. Sometimes, this incorrect dosing of chemicals may also damage the walls, especially if they involve acids or peroxides.
- Foot Valve: As the name suggests, this is a one-way or a non-return valve that is attached to the line of suction. It is mostly positioned at the product drum. A float switch is attached to it to check the availability of the product. This switch raises alarm when the product runs out.
- Dosing Line: This is mainly a hose made of different robust materials such as PVC, PE, or stainless steel. These materials make it suitable in unfavorable conditions.
- Control System: Today, most plant owners utilize software and control systems to ensure the appropriate functioning of the pumps. These control systems also help automate the pumps for better functioning. Sensor-driven central control systems and SCADA systems are used for the purpose. Sensor control systems are designed to detect the levels of chlorine, pH, and other substances.
A Few Variants of Dosing Pumps Used in Industries
Like any other industrial pumps, these dosing pumps are differentiated based on their purpose and their typical actions. They are designed for dosing different chemicals at different pressures. The following are the three important variants of dosing pumps based on their purpose and action.
- Diaphragm Pumps: The pumps use diaphragm mechanism, which is why they are named diaphragm pumps. There are two types of diaphragm pumps – a constant injection type pump and a pulse injection type pump. Both these pumps use diaphragm mechanism. Diaphragm constant injection pumps have valves and pistons on the outlet and the inlet. The piston can empty and fill the chamber, by drawing out or in. The chamber fills when the piston is drawn in. A chemical is injected in a specific dose and at a predefined speed. On the other hand, diaphragm pulse injection pumps are fitted with a solenoid coil, which injects chemicals in pulses. These pumps have simple designs and are inexpensive.
- Lobe Pumps: These pumps feature meshing gear impellers. They send a prefixed volume of chemicals through these impellers. Lobe pumps are suited for fluids having high viscosities. These pumps are not designed for low flow rates.
- Peristaltic Pumps: Of all the pumps mentioned on this list, these are the most accurate dosing pumps used today. They feature flexible bent tubes, which allow the fluids to pass. A roller in the pump helps control the flow of fluid.
A Glance Through Various Applications of Dosing Pumps
Metering pumps are used in a variety of industrial, commercial, municipal, and maritime applications. They are used for water treatment applications in the following industries:
- Agriculture
- Dairy farms
- Horticulture
- Breweries
- Food service and food processing
- Power generation
- Oil and gas
After understanding the working and importance of dosing pumps, you might have realized the significance of sourcing from a trusted supplier. Cannon Water Technology, Inc., is one of the leading providers of dosing pumps such as diaphragm and peristaltic pumps of industry-leading brands.