Effective Cooling Tower Shutdown Tips Offered
Posted by David Cannon on 10th Jun 2021
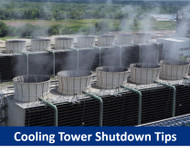
A cooling tower is one of the most popular heat exchanger devices used in various industries for cooling hot water, which is produced during several manufacturing processes. The hot water is led to the cooling tower through pipes and brought in contact to air, which absorbs heat from it. This creates cold water for circulation within the tower. Cooling towers are commonly used in petrochemical and oil refineries, nuclear power stations, thermal power stations, and similar applications. The cooling towers are generally used during spring and summer for heat exchange. These devices are usually shut down during the fall and winter seasons to avoid the risk of corrosion and microbial growth. These towers may possess stagnant water, which serves as a breeding ground for bacteria called Legionella and may cause its outbreak when the tower is restarted in spring.
Preparing your cooling tower for seasonal shutdown requires certain planning. This post offers easy-to-follow steps for your cooling tower shutdown.
How to Prepare Your Cooling Tower for Seasonal Shutdown
The below-given steps will help you prepare the cooling tower for the seasonal shutdown. This helps ensure the system remains protected through the winter and fall season and starts easily in spring. For ease, this section is divided into two parts – steps to be performed before the cooling tower shutdown/layup and steps to be performed during the cooling tower shutdown/layup.
Steps to Perform Before the Cooling Tower Shutdown/Layup
- Increase the bleed to the tower at least two to three days prior to the cooling tower shutdown. This increase in bleed helps in the removal of any suspended solids that get accumulated in the system during regular operation.
- Try to remove the scale deposits from drift eliminators at this time. This is perhaps one of the most effective ways of cleaning your cooling tower before the shutdown.
- Do not forget to add additional corrosion inhibitors to the cooling tower as they help protect the system during the off-season.
- Next, adding a scale and sludge dispersant will help remove any scales and accumulated dirt.
- After this, add twice the amount of non-oxidizing biocide and let it circulate for the next 5-6 hours. If you cannot find a good quality non-oxidizing biocide, an oxidizing biocide can also be used as an alternative. This step is performed to remove biofilm. It also helps sanitize the cooling system.
Steps to Perform During the Cooling Tower Shutdown/Layup
There are two types of cooling towers – counterflow and crossflow. In crossflow towers, the water flows vertically through the fill and the air flows horizontally. In crossflow towers, the air flows in the vertically upward direction to counter the flow of water.
- If you are using a crossflow tower, then take care to sweep off the hot water distribution basin. If you are using a counterflow cooling tower, you can remove the drift eliminator and inspect the nozzles. This must be done when the tower is in operation and it helps identify clogs. If you identify clogged nozzles then take care to replace or clean them.
- Remove all the strainers and clean them. You need to reinstall them after cleaning.
- Shut down the controller but ensure you do not remove its power source. Simultaneously, you must take steps to remove, as well as protect the conductivity probe of the tower.
- Next, refill the system. Having said that, you need not refill the tower system to the operating level. Along with this, you can vent the chillers and check if they are filled with water completely. After this, take care to close all the vents.
- Next, you must perform water treatment to the whole tower. During this process, take care to recirculate the system for the minimum time of 8 hours and use all pumps during the process.
- Take care to drain the pump completely from its lowest point.
- Clean the chemical feed pumps and flush them remove any contaminants. After this, put the foot valve of pump in water and operate the pump. This will help flush out the components of products used for treatment. You can keep the foot valve out of the tank until spring.
- Check the end bells of the chiller condenser and brush their tubes. This helps remove any stagnant water in water chiller. Thus, it must be performed properly.
- Store the chiller without end bells when they are not in use.
The above steps will not only help prepare you for cooling tower shutdown and ensure a worry-free fall and winter. It is important to use the right and quality cooling tower treatment solutions during the pre-layup and layup stage. These solutions must be sourced from trusted suppliers or leading brands for effective results. Cannon Water Technology provides various cooling tower equipment and cooling tower treatment solutions developed by the brand. These treatment solutions have been effectively used for corrosion inhibition, as well as scaling control for several years now.