Know How to Choose the Right Corrosion Inhibitor
Posted by David Cannon on 2nd Dec 2019
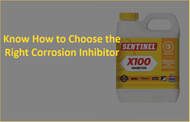
There are many applications such as pumping systems used for wastewater or chemicals, where metals are exposed to harsh environment and could be corroded. Once rusted and corroded, the metallic parts or systems can’t be used and pose risks, and hence developing corrosion resistance in any product, part, or a system is extremely crucial for its proper functioning. A corrosion inhibitor is a substance that prevents or reduces the impact of corrosion on an exposed metal in a harsh environment such as chemical or mining. They are added water or acids in specific concentrations to form a film or coating, which acts an inhibitor. This post talks about various types of corrosion inhibitors and the factors you should consider when choosing one for your application.
What Are the Different Types of Corrosion Inhibitors?
There are various methods of corrosion inhibition; however, the application of corrosion inhibiting substances is the most convenient, and acts as the first line of defense. Here are a few types of corrosion inhibiting substances:
- Anodic Inhibitors: These type of inhibitors form a film at the metal-electrolyte interface to prevent corrosion. The basic principle of these substances is surface adsorption or forming a thin film on the metal surface, which influences anodic polarization properties to curb corrosion. This thin film blocks the electrochemical reaction which stops the metal such as iron from dissolving in the solution. Chromate, tungstate, molybdate, and nitrate compounds are a few examples of anodic inhibitors.
- Cathodic Inhibitors: These inhibitors follow the same principle to curb the electrochemical reaction at the cathode end. Organic compounds such as calcium compounds of phosphonates and polyphosphates, zinc ions, naphthols, phenolic compounds, gelatin, and tannin are widely used as cathodic corrosion inhibiting substances. Cathodic inhibitors produce a non-conductor insoluble compound, which forms this protective layer over the metal surface.
- Mixed Inhibitors: Certain commercial applications require mixed inhibitors. Chromate, phosphonates, and polyphosphate compounds of zinc act well as mixed inhibitors. These substances curb the anodic as well as cathodic corrosion process. Silicates are also used as water softeners to stop the formation of rust in water.
- Volatile Corrosion Inhibitors (VCI): In this process, volatile compounds such as hydrazine are used to prevent corrosion in closed systems such as condenser tubes. VCI compounds are volatilized and transferred to the corrosion sites in a closed environment such as boilers. When steam is formed these compounds are transferred along with it to the condenser tubes.
Factors to Consider When Choosing a Corrosion Inhibitor
While the choice of the corrosion inhibitor largely depends upon your application requirements, here are a few factors you may want to consider when buying one:
- While reading more on the topic will give you a lot of insights, you can actually search for experts in this field who have patented technologies to make these inhibitors.
- Consider the type or materials or metals your systems have and the probability of corrosion happening or metal exposure at particular sites.
- Consider the timeframe and the duration of the day these systems such as boilers and industrial water treatment units are being used They may be used for one week or one month, or sometimes a few hours on each day or on specific days. The concentration and type of inhibitors can be decided accordingly.
- Address the external environment, weather conditions such as temperature, humidity, and the probable exposure of these metals to extreme heat or cold.
- Take into consideration the safety requirement of workers and probable damage to systems and the manufacturing unit as such.
- Check how much these systems are handled by humans. It is essential to note fingerprint impressions, or any other substances on our palms and finger such as cream, oil, and germs. Based on most of these factors, you can decide the amount of coating required.
If you are looking for high-quality corrosion-resistant pumps, motors, or related equipment for your application, ensure you source them from a reliable supplier who sells known brands. Cannon Water Technology is one of the reliable distributors of superior quality chemical pumps of several brands and types. The company also provides various types of chemical-based corrosion inhibitors for heat exchangers, boilers, and closed systems.